Underwater wet welding electrode, CEWELD AquaForce
Underwater welding electrodes are meticulously engineered for welding tasks performed under a variety of ambient conditions where the workpieces are submerged underwater. The composition of these electrodes are initially made for dry welding. CEWELD AquaForce, on the other hand, has been specially developed for wet welding. This is why AquaForce is the #1 electrode for underwater welding. Let's explore what makes AquaForce so good!
Traditional (underwater) welding electrodes
most commonly used underwater electrodes are made with a mixture of the following elements:
SiO2 | FeO | Al2O3 | TiO2 | ZrO2 | MnO | CaO | MgO |
---|---|---|---|---|---|---|---|
17 | 43 | 11 | 18 | 1 | 8 | 2.8 | - |
A blend of these elements are mixed into a paste, enriched with waterglass, and subsequently compressed onto an unalloyed steel core wire. The substantial iron powder content in this coating categorizes the electrode under the dry welding classification; AWS A 5.1 E 7014. Traditionally, the composition of E 7014 electrodes is optimized for dry welding applications and was not designed for wet welding. There hasn’t been a viable alternative, until now!
CEWELD AquaForce


Ceweld AquaForce underwater welding electrode is different!
CEWELD AquaForce is a completely different electrode and is not based on Iron powder. Iron powder (FeO) is an unwanted element for wet welding because it reduces impact strength, in-stabilizes the arc behavior, promotes hydrogen content, and results in rough concave weld beads when welding underwater.

Weld economy on filled welds
Using a 3,2 mm electrode results normally in an A height of approx. 3,5 mm and especially in PB, PE and PG position the weld shows a concave shape that is sacramental to the strength of the weld. AquaForce is engineered to offer a perfect flat shaped weld in all positions with a minimum a height of 4,0 mm!
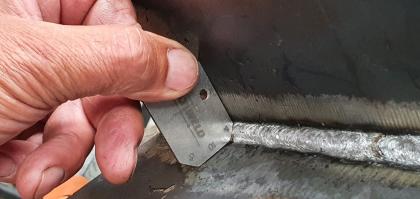
"AquaForce MG Filled weld in PG position with excellent penetration and flat bead appearance"
Due to the fast-freezing properties underwater the bead surface has no time to slowly create a smooth fine rippled surface, in practice this results in slag that is not easy to detach. AquaForce is formulated to create a slower freezing weld pool with a much more stable arc to obtain a bright smooth surface that is not able to stick to the slag. As a result, the slag practically removes itself.
When welding multiple layers it is necessary to grind between the layers to avoid porosity and inclusions, AquaForce however does not need cleaning between the layers and leaves finally rippled beautiful welds.

"Making hight Quality underwater welds, Aquaforce"



The perfect coating that solves numbers of problems
AquaForce is dipped in a fully automated way using a unique coating that burns at lower temperature without leaving residues in the water. When exposed to sun during summer no damage is caused and AquaForce can be stored for a very long time without loosing its unmatched welding properties.

Final coating for electrical insulation and moisture protection
During the years many final coatings have been applied on underwater electrodes to prevent the coating get wet and at the same time isolate the electrode against electric shock for welders safety. Some brands are using Acryl paint, some use Alkyd type of paint and others tried there luck with vinyl paint and even paraffin has become a common material to use for isolating underwater electrodes.
New customers are invited to take advantage of a special offer: 50% off your initial purchase of AquaForce!